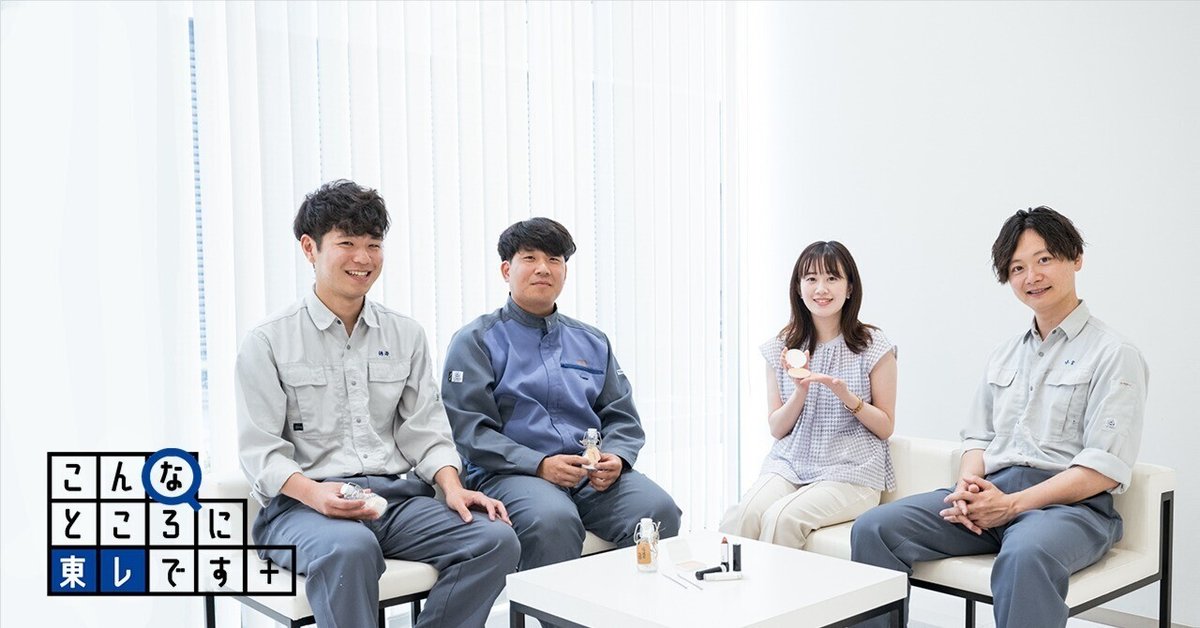
「なめらかな肌触り」をもつ化粧品。その未来を担う新ポリマー微粒子誕生に挑む若き社員達の軌跡
暮らしを支え、暮らしを見守る東レ製品。オフィス、家庭、街…実は、さまざまなところで使われている東レの“素材”をもっと知って欲しい。そんな想いでスタートした連載企画「こんなところに東レです+」。企画、開発、製品づくりなど東レのものづくりを支える「人」の魅力にフォーカスしながら、東レの“素材”をご紹介します。
化粧品のファンデーションやアイシャドウなどに、柔らかな肌触りといった官能性や滑り性を付与するために使われてきた東レの真球状ポリアミド12微粒子。国内外の高級化粧品市場において、長年東レはトップシェアを貫いてきました。
しかし、近年世界中で環境意識が高まるなか、より環境負荷に配慮した新たな素材が求められるように。そこで東レの長い基礎研究の歴史と知見を武器に、これまでにない新素材の開発に乗り出しました。
そして誕生したのが、ポリアミド12微粒子と同様になめらかさを追求しながらも、生分解性を有するポリアミド4微粒子です。既存技術では微粒子化するのは非常に困難な特性を持つポリアミド4ですが、研究者と技術者、営業担当がタッグを組み、苦難を乗り越えてついに開発に成功。ポリアミド4微粒子が生まれた背景や研究から形になるまでの道のり、研究開発に込めた思いについて話を伺います。
世界初、生分解性の高いポリマー微粒子。ポリアミド4微粒子の誕生
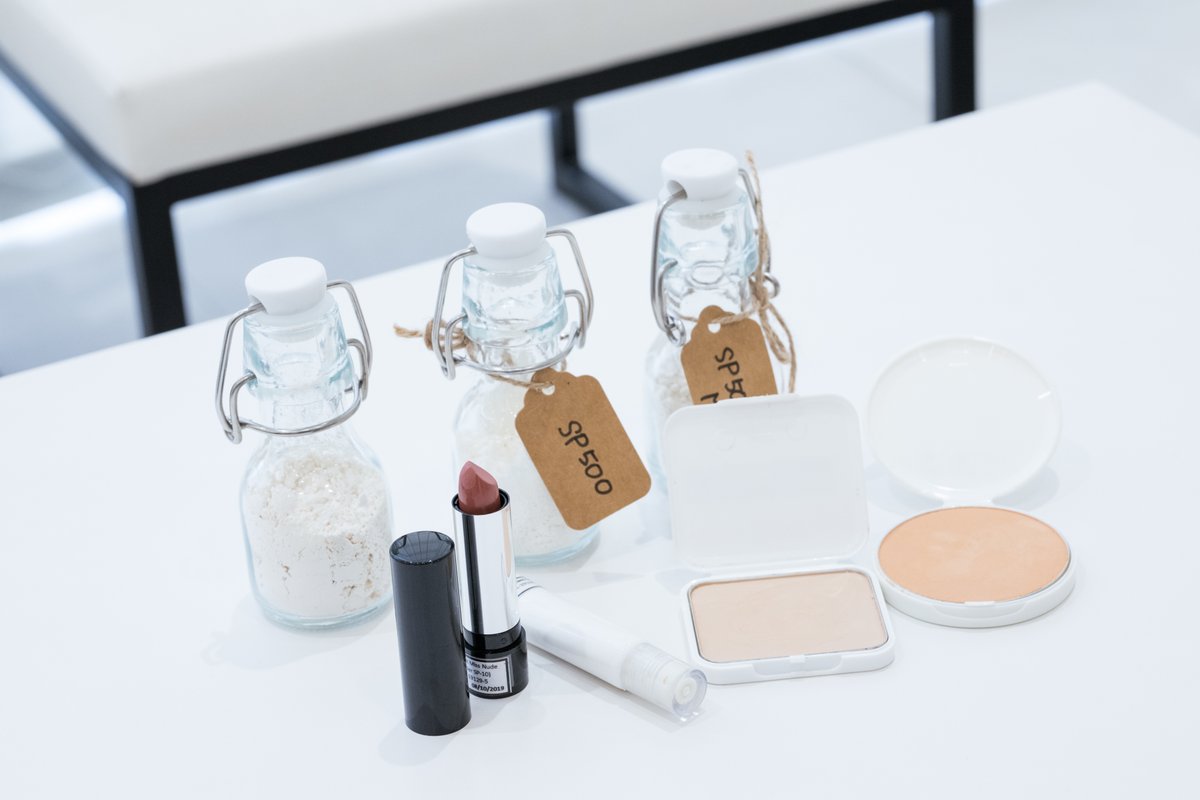
―ポリアミド4微粒子が開発されたきっかけや背景を教えてください。
小宮 健(以下、小宮(研究)):もともと東レには1970年代からずっと販売しているポリアミド12からできる微粒子パウダーがあります。このパウダーが本当によくできたパウダーで、当時から処方や作り方も大きく変わらず、これに代わる材料はないというくらい高級化粧品業界において長年重宝されてきました。そんななか、時代のニーズに合わせてより環境負荷を減らす新しい素材を生み出していこうというところが開発の起点です。そこで注目したのが、生分解性のあるポリアミド4でした。
―そもそもポリアミド12微粒子は化粧品の中でどういうところに役立っていたのでしょうか?
柴田彩友美(以下、柴田(営業)):いわゆる感触改良剤として使われます。パウダーファンデーションだけでなく、リキッドファンデーション、日焼け止め、一部の口紅、あとはクリーム類にも。肌馴染みがよく滑り性がよかったり、塗ったときの塗り広がり性がよかったり。感触を付与することが目的です。
―それに比べて、ポリアミド4微粒子はどんな特徴がありますか?
小宮(研究):簡単に言うと、ポリアミド12微粒子と同様に、肌馴染みがよくなる滑り性などの感触を付与することができる特徴がありながら、「生分解性」があるということです。
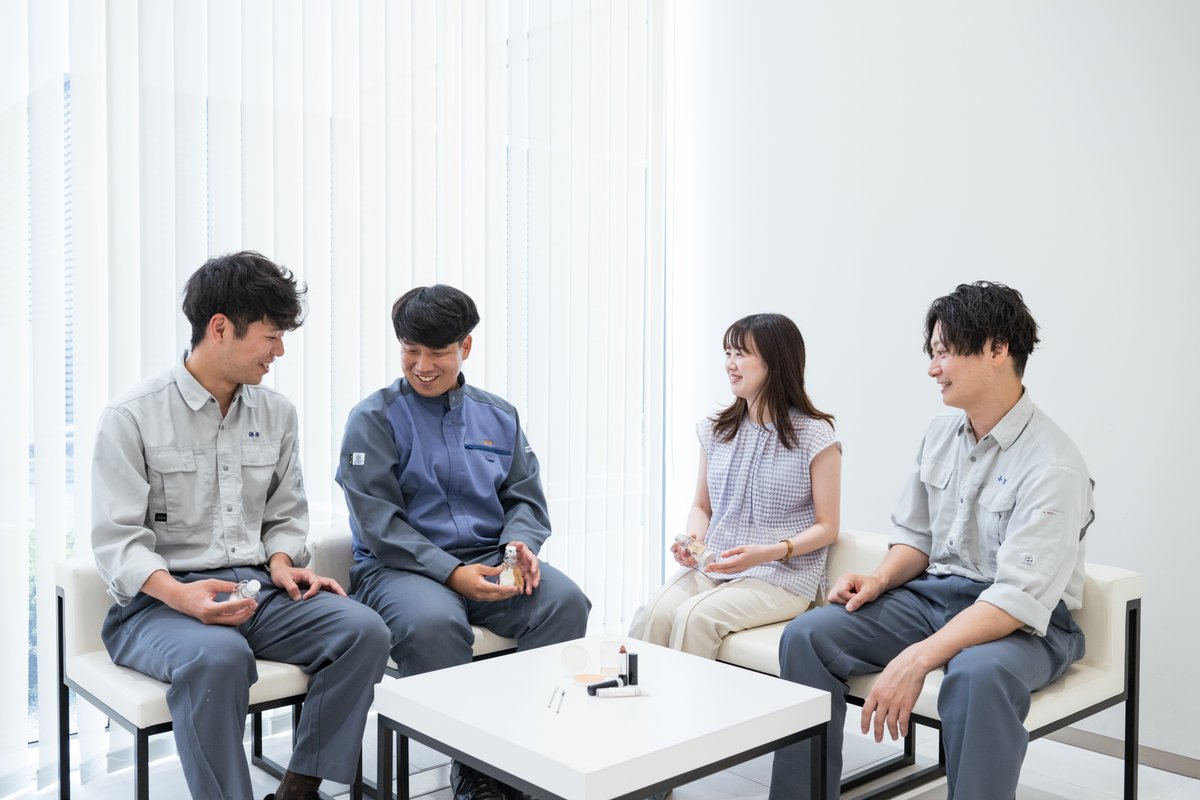
―このチームはいつから始動したのですか?
羽柴(技術):私が所属していたケミカルプロセス技術部にテーマがきたのが2021年の7月。それまでは小宮さんがずっと1人で何年も基礎研究を続けてきました。
徳海裕也(以下、徳海(技術)):僕は今年の3月にケミカルプロセス技術部内の異動で、このチームに加わりました。ちょうどメンブレン技術部へ異動になった羽柴さんの後任として引き継ぎました。
まずぶつかったのは、「粒子化が難しい」という壁
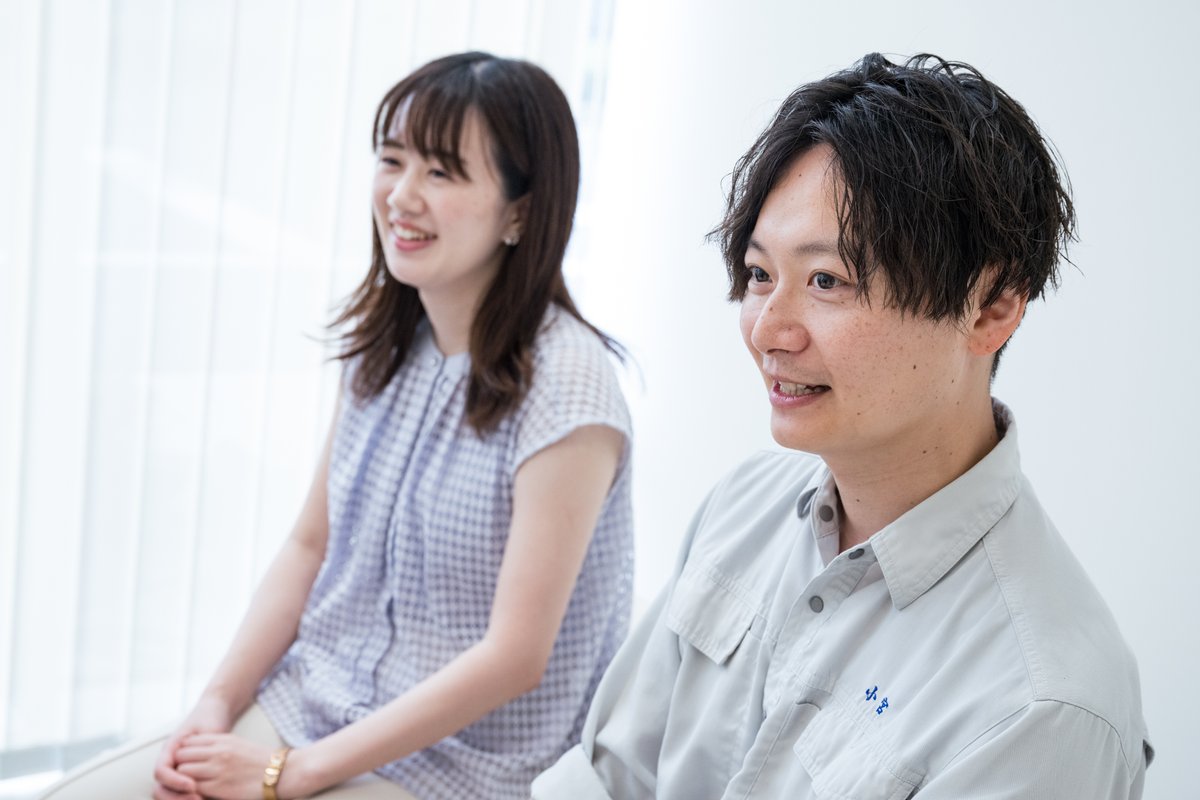
小宮(研究):実はこのポリアミド4は、もともと昔から東レで基礎研究をしていた素材なんです。生分解して環境へ優しく環境負荷を下げることと、ポリアミド12の微粒子に近い物性を持つことを考えると、粒子にするハードルが高いけれど、社会からのニーズにも合致していて全体のバランスもよかった。東レが長年蓄積してきた技術や知見の活用であり、日の目を見なかった研究を形にする機会でもありました。
―粒子化するハードルが高いとはどういうことでしょうか?
羽柴晃輝(以下、羽柴(技術)):ポリアミド4は、ちょっと特殊な特徴があります。それは熱分解性があるため高温での加工が難しいこと。そして、合成が難しいこと。つまり、粒子にするのがすごくハードルが高いということです。ポリマーを粒子にするためには、熱を加えて一度溶かしてから粒子にする方法が主流ですが、ポリアミド4は熱を加えると分解してしまう。開発ではこの課題を乗り越えることが一番大きなハードルでした。
―粒子化するハードルはどう乗り越えたのでしょうか?
小宮(研究):開示できない技術が多いのですが、東レのナノアロイ技術を参考にしました。これは異なるポリマー同士を混ぜてその混ざる様態によって特殊な性能を持たせる技術。一見粒子と関係ない技術を当社の粒子化技術と融合することで、ブレイクスルーを達成できました。手応えも感じ始め、ようやく話が動き始めました。
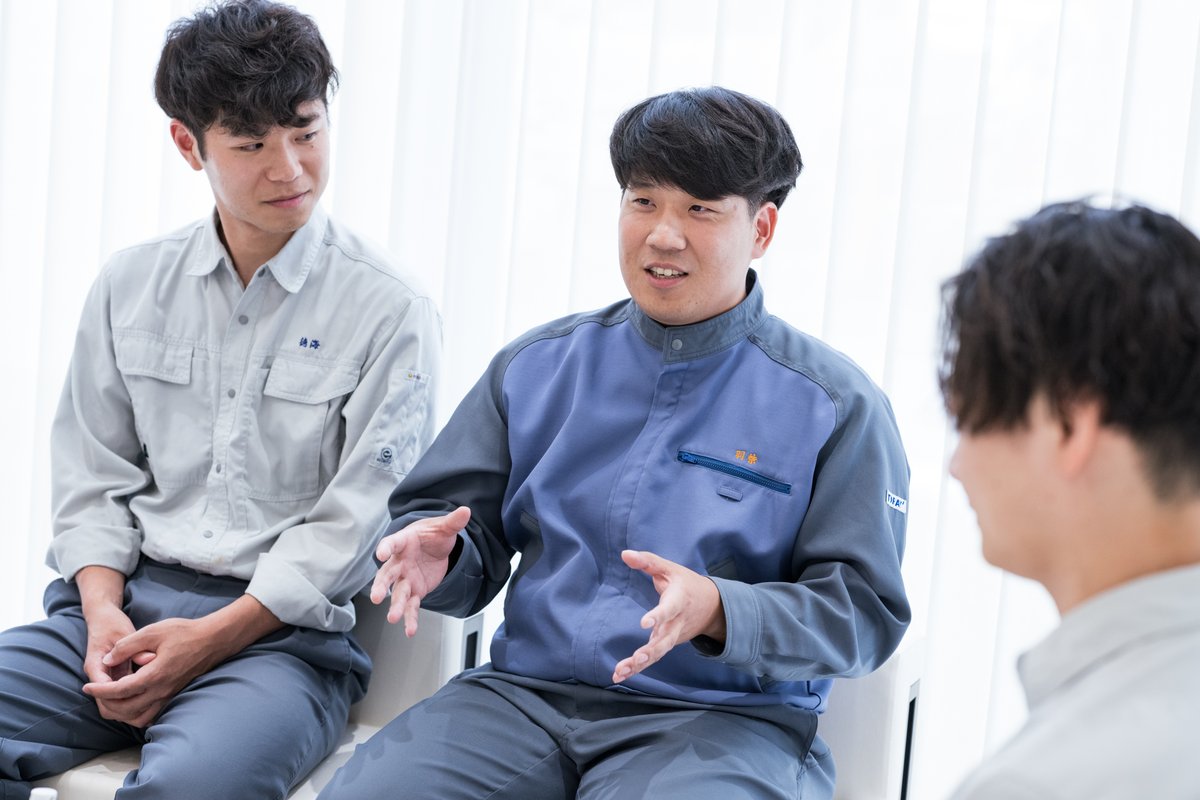
―羽柴さんは、まずこの案件への依頼があった時どんな印象でした?
羽柴(技術):2020年に入社してケミカルプロセス技術部に配属なった時、上司からポリアミド4微粒子の開発について聞いていたんです。「その開発をするときが来たら、絶対僕にやらせてください」と希望を出していました。全く新しい物質を世に出していくという仕事をぜひやりたいと思ったんです。
2020年5月に配属されて、話が来たのが2021年の7月。実際に小宮さんから実験風景を見せてもらったり技術を教えてもらったり。技術部では研究で作った数グラムをどうやったらもっと大きな設備で作れるのかというのを実験室で試しながら、計算して組み立てていきました。
―そこからは順調にスケールアップできたのですか?
小宮(研究):それが…。苦戦した球状化もクリアして、やっとこれでいける!と羽柴さんにも共有して、進めていたのですが、実際に量産へ向けてやってみると、その方法では実はすごく効率が悪いということがわかってきて…。
羽柴(技術):長い目で見るとこのまま進めてもいずれ壁にぶつかるから、今ここで一旦立ち止まろうと仕切り直しを決断したんです。だいぶ終盤の段階だったので、迷う部分もあったのですが、小宮さんに一度持ち帰ってもらい、まっさらな状態で考え直してもらいました。
その結果、「今度こそいける!」と光が見えてきた。いよいよ数十キロ作ってみようとバタバタ動き始めたのが昨年のことです。入念に準備を重ねて、名古屋事業場総動員で作ったのが11キロのポリアミド4微粒子。そこからいっきにスケールアップしていきました。
―「スケールアップの大変さ」はどういうところにあるのでしょうか?
羽柴(技術):1Lや500mlのガラス容器の中で数十ミクロンの小さい粒子を作るのが実験室のスケール。それをスケールアップするっていうのは、天井の高さくらいあるような大きな容器の中で同じ大きさのものを作るということ。数百mlの容器の中で5ミクロンの粒子を作るのと、1000Lの容器の中で同じ5ミクロンの粒子を作るのとでは、単純に掛け算すればできるというわけではないんです。そういったところを入念に計算をして、いろいろな条件でテストしながら見極めていかないといけません。
―なるほど。最初に11キロ作ることができた瞬間ってどんな気持ちでしたか?
羽柴(技術):ニヤっとしましたね(笑)。最初は濡れた状態でトレーに入れて大きな乾燥機で乾かすのですが、乾燥機の大きな扉を2人がかりくらいで開けてホカホカの粒子を見た瞬間、「ついにここまできたか」と感動しました。最初は夢物語のようだったことを、小宮さんが現実に近づけてくれて、気づけば大きく前進していました。
小宮(研究):僕の妄想から始まって自分だけでは数グラムの世界が、みなさんの協力で本当に数十キロというスケールまで持っていくことができた。何度も壁にぶつかりましたが、乗り越えられたのも技術のみなさんがいたから。さらに営業がそれをメーカーに売り込んでくれる。チームが一丸となったからこそ成し遂げられたと思っています。
いよいよプレスリリース。量産化に向けてスタート
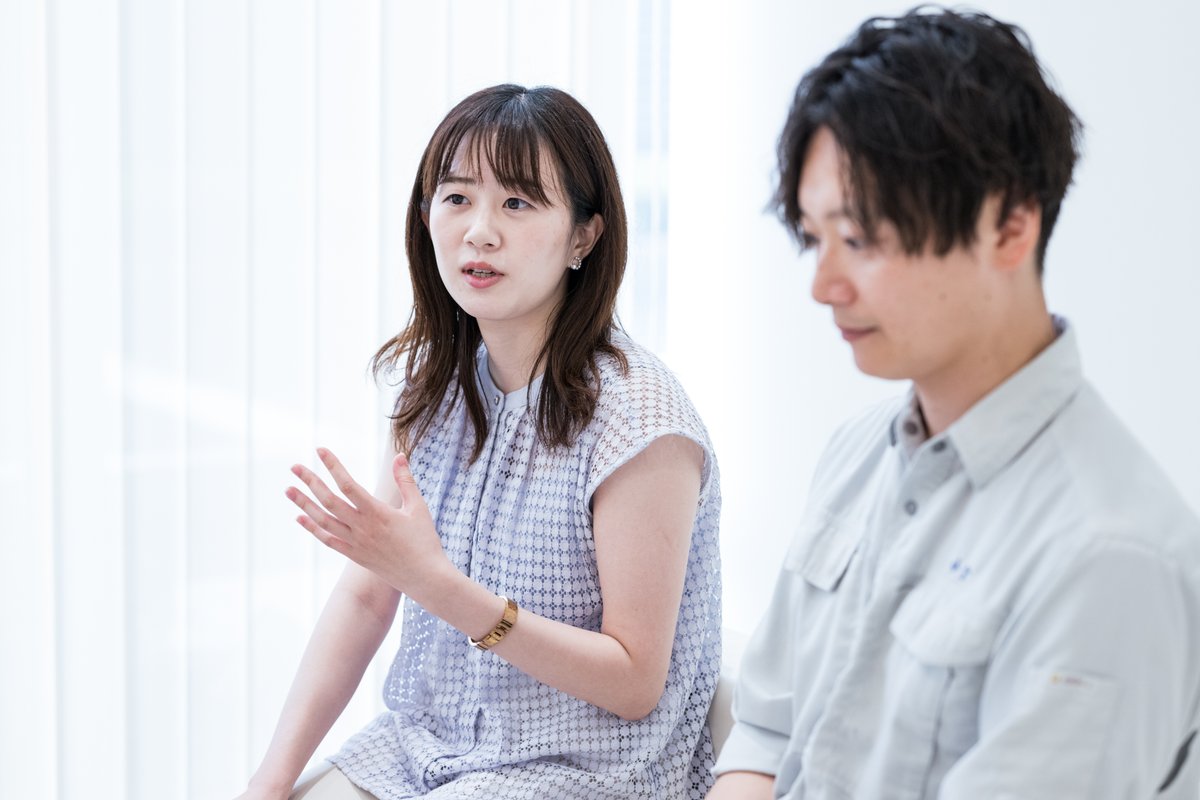
―営業として、柴田さんはいつから関わっていますか?
柴田(営業):正式に担当になったのは昨年10月からです。ここまでの大きな開発に混ぜてもらえる嬉しさはもちろん、一方で大きな不安もありました。小宮さんも羽柴さんも相当な熱量でやられているし、当然予算もかかっているなかで、これをなんとか形にして世に出さなくてはいけない。売らなきゃいけないという思いと義務感。日々それを意識しながら、各所と連携して取り組んでいます。
―みなさんの努力が実りかたちになったポリアミド4微粒子ですが、先日、世界へもお披露目されたのだとか。
柴田(営業):はい。4月にパリで化粧品の世界最大の展示会がありました。化粧品だけでなく原料や技術が展示され、世界各国から人が集まります。やはり生分解という点は注目を集めましたね。触ってもらい感触の良さも知っていただく機会になりました。確実にニーズはあるなと確信できました。
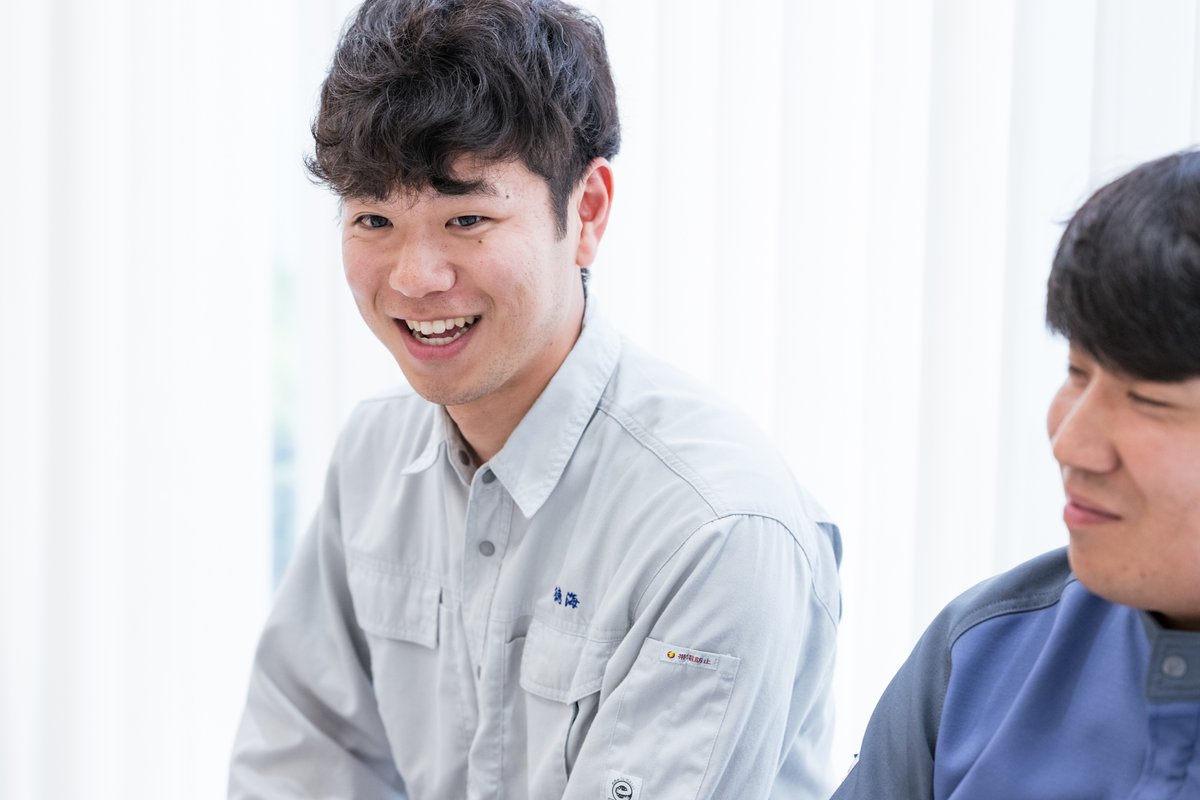
―実際の製造や量産化については、現在は引き継いだ徳海さんが奔走されているようですね。
徳海(技術):そうですね。ある程度技術は固まってきているのですが、実際にどういった設備で作るのかというところは絶賛検討中です。今は体制作りが大きい課題の1つです。
柴田(営業):この微粒子ができるまでにいろいろな工程がありますから、その各工程をどこで行うのかを検討していく必要があり、今詰めていただいているところです。
小宮(研究):言葉で聞くと簡単な話に聞こえるかもしれませんが、1つ1つしっかりと詰めていかなくてはならない部分。製造場所の選択肢もたくさんありますし、その中で最適解を探っていくというのはものすごく大変なことなんです。ここまで技術ができあがってきても、最後の詰めのところでうまくいかなければ、結局実現できないので重要な段階でもあります。その全部の流れを徳海さんが考えてくれているんです。
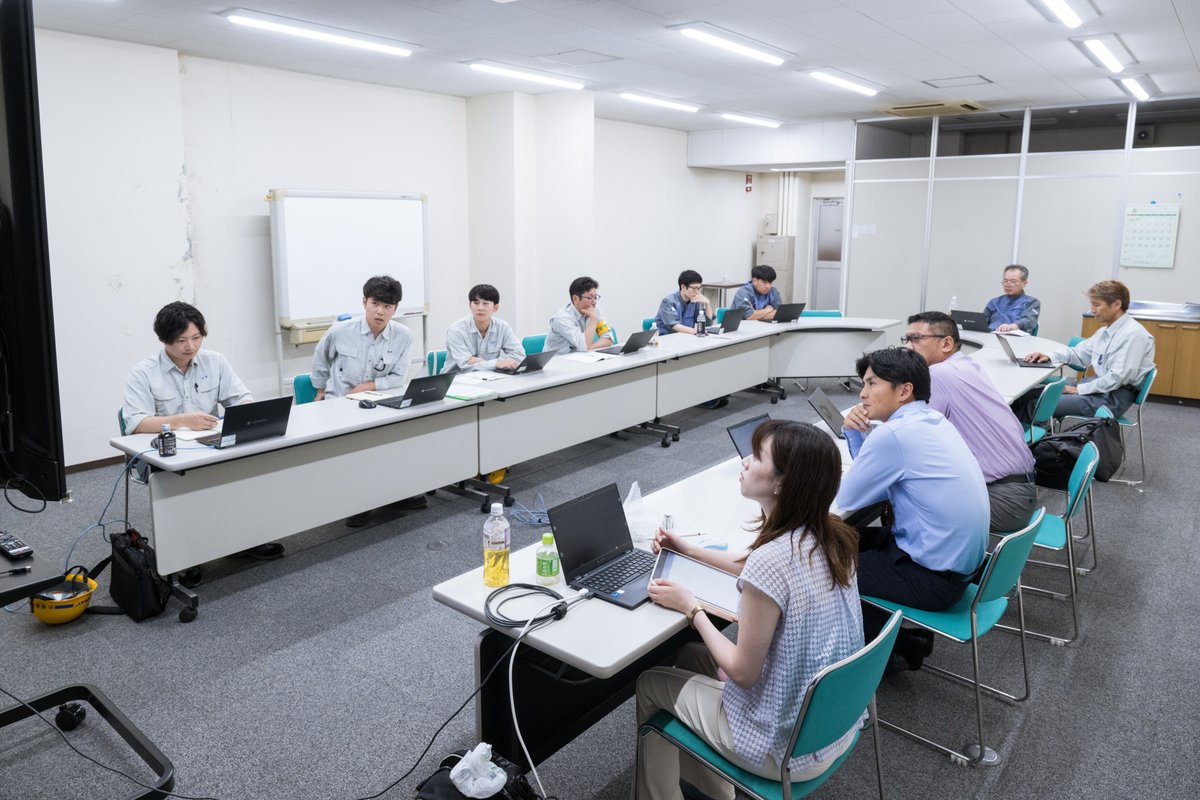
―技術の方はそういったところまで担当されるのですね。
徳海(技術):そうですね。技術開発もそうですが、実際に製造に至るまでの体制を構築するところも技術の仕事です。対応できる設備のチョイスもそうですし、それを持っている場所が、実際に製造をやってくれるのかどうかという話にもなります。バランスが重要というか。いろいろな人と関わって、何が最適解なのかを見定めながら、実現していきたいと思っています。
―素材の開発ができたらゴールというわけではないと。
徳海(技術):そこからがスタートというか…。実現するまでにいろいろな障壁があるので、きちんとクリアにして、進めていく必要があります。各所との調整も頭を悩ませるところですが、そこはもうやや強引に、空気をあえて読まないようにしています(笑)。最後に僕がこのプロジェクトを台無しにすることがないよう責任感をもって、言うことは言うスタンスで仕事をしています。
熱い思いを胸に、駆け抜けたチーム
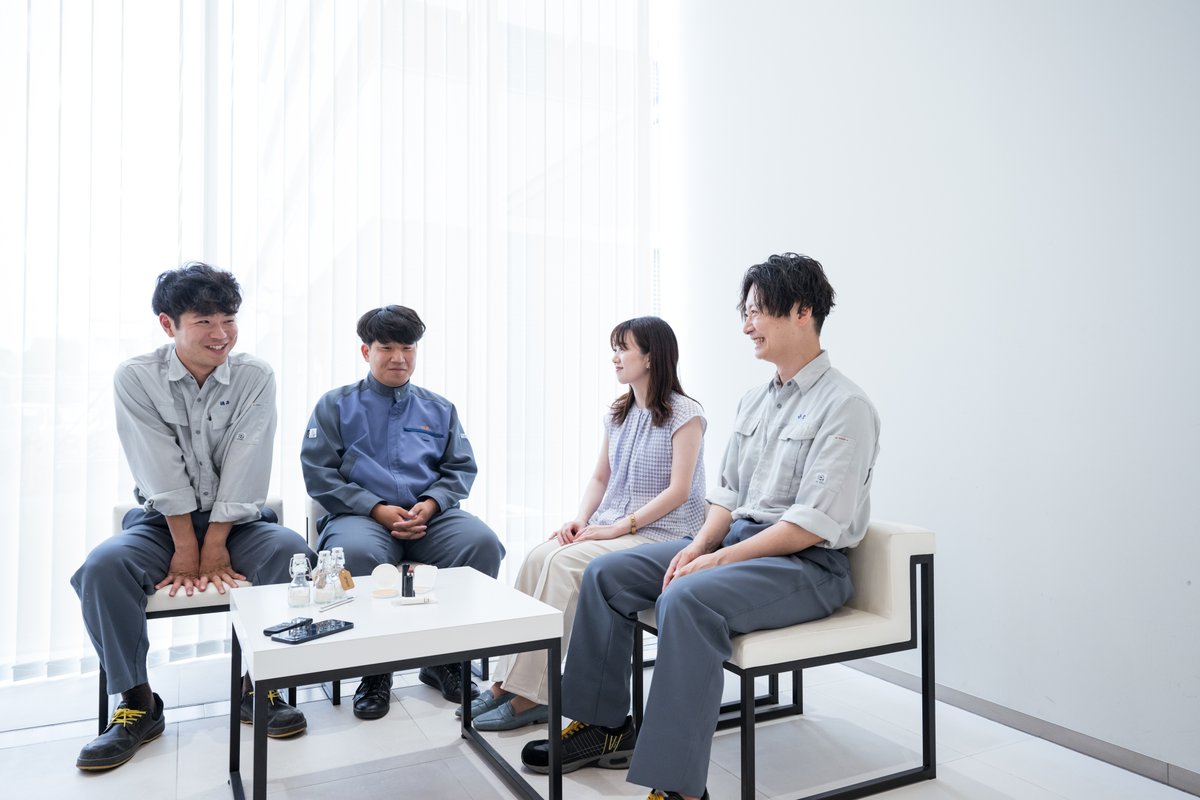
小宮(研究):本当に、羽柴さんと徳海さんと柴田さんの3人じゃないと、こんなにスピーディーには進まなかったと思うので心強いです。
羽柴(技術):たしかに大変ではありますが、みんなこの仕事に対して根底に楽しいとかワクワクする気持ちがあるから頑張れるのだと思います。
柴田(営業):それはありますね。私は文系なので、正直理解が難しいところもあるんですが、月1回の進捗会議で、いとも簡単そうに「こんなことができました。新しい方法はこれです」みたいに報告してくださる姿に毎回驚いています。よくよく聞いてみると、本当にすごいことをしているんだなと感心しています。何よりみなさん熱いので、私も気合が入りますね。
小宮(研究):開発状況についてお互いに思いのたけをぶつけ合って、ああでもないこうでもないと語り合うこともあります。飲みながら熱く語っているうちに気づいたらもう夜中の3時なんてことも(笑)。
柴田(営業):そんな熱い思いに触れられるというのは楽しいですし、贅沢な経験。世にないものをゼロから生み出して、それを売っていくという可能性が未知数でワクワクすると同時に、生かすも殺すも自分たち次第なのだと責任感も生まれました。
チームだったからこそ得られた大きな気づきや学び
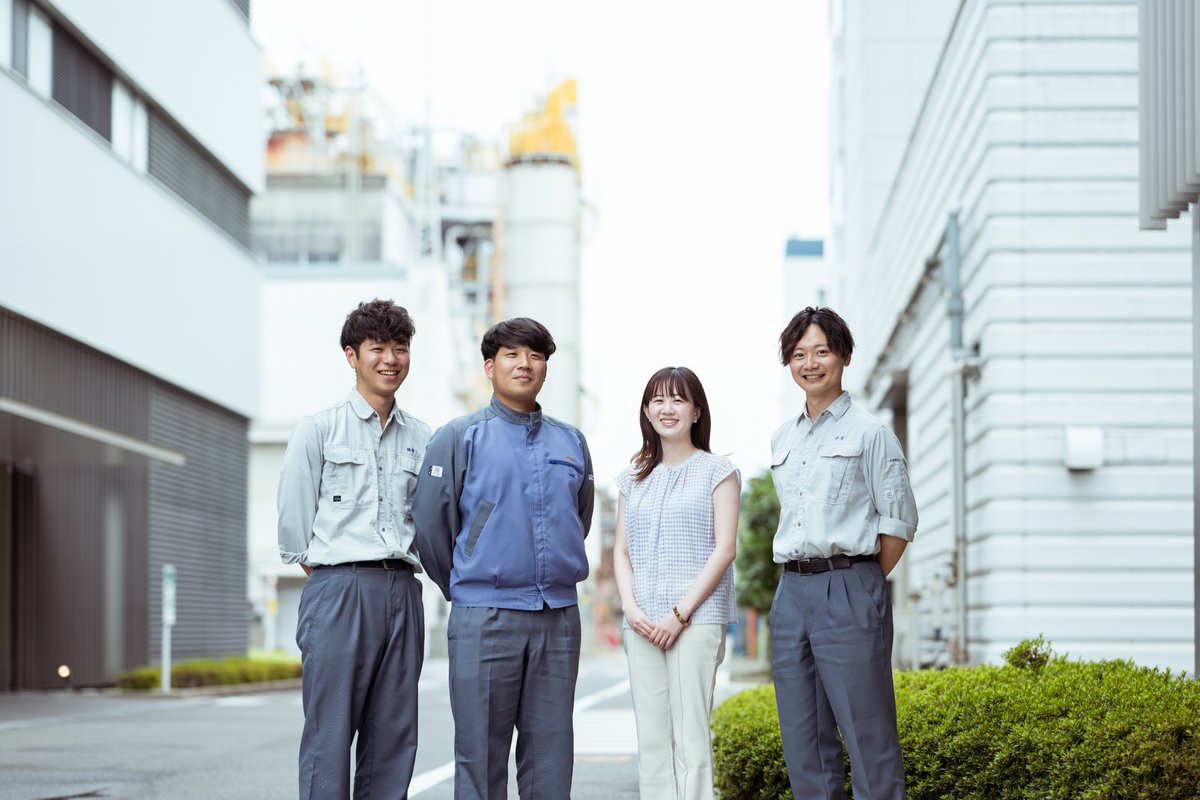
―完成まではもうひと頑張りのところですが、このプロジェクトに携わったことでみなさんの学びになったことや気づき、今後のお仕事に生かしていきたいことを教えてください。
小宮(研究):今回、僕個人としてもこんなゼロベースからスタートしたのは初めてのことだったし、ここまでのスケールの開発は本当に良い経験です。うまくいった部分もありますし、後から考えるとこういう進め方じゃないほうが良かったなと反省する部分もあります。今後に生かしながら、新しい素材の研究開発や、またゼロから作りあげることをやっていきたいなと思います。
何よりもこうやってチームで動くのも研究者としては珍しい環境で新鮮でした。働き方の幅も広がったし、何より自分自身の視野も広がったと思います。
柴田(営業):営業として他の案件もありますが、ここまで新しい開発に研究と技術とワンチームで携われるのは、そう多くありません。せっかくメーカーの営業としてものづくりに関わっているので、この経験を生かしていきたいと思っています。お客さまの要望に合わせた商品を提供するだけでなく、1から考えた製品が完成し、それをお客さまに向けて営業、販売、管理、流通など一連の流れを見ることができるのも今回の大きな学びです。
羽柴(技術):「新しいものを世に届ける」という体験は今回が初めて。営業、研究、技術の3者でタッグを組んで1つの目標に向かって走っていく「ザ・開発プロジェクト」みたいな案件に携わったのも初めてです。自分自身の成功体験の1つになったかなと思っています。
さらに新しい領域にチャレンジしたい気持ちが芽生え、一足先に離脱して、今は新しい部署でもともと学生時代にしていた逆浸透膜の研究に注力しています。これからも同じように技術開発をやっていくなかで、今回の経験を糧にして頑張っていきたいと思っています。
徳海(技術):この業務を通して、物事を決める要所、要点を捉える能力が非常に上がったなと感じています。さまざまな立場の人たちが何を気にされているのかとか、ネックになっていることはなんだろうとか、事前に自分で考えておくことが重要だと実感しました。
これを機に、開発でもプロジェクトでも物事を回して円滑に動かしていく役割を今後もやっていきたいと思っています。技術者として技術力を上げることも大事ですが、全体をうまくまとめあげて、1つの目標に向かって舵をとりながら駒を進めていくおもしろさを、今回の案件を通して感じました。
【プロフィール】
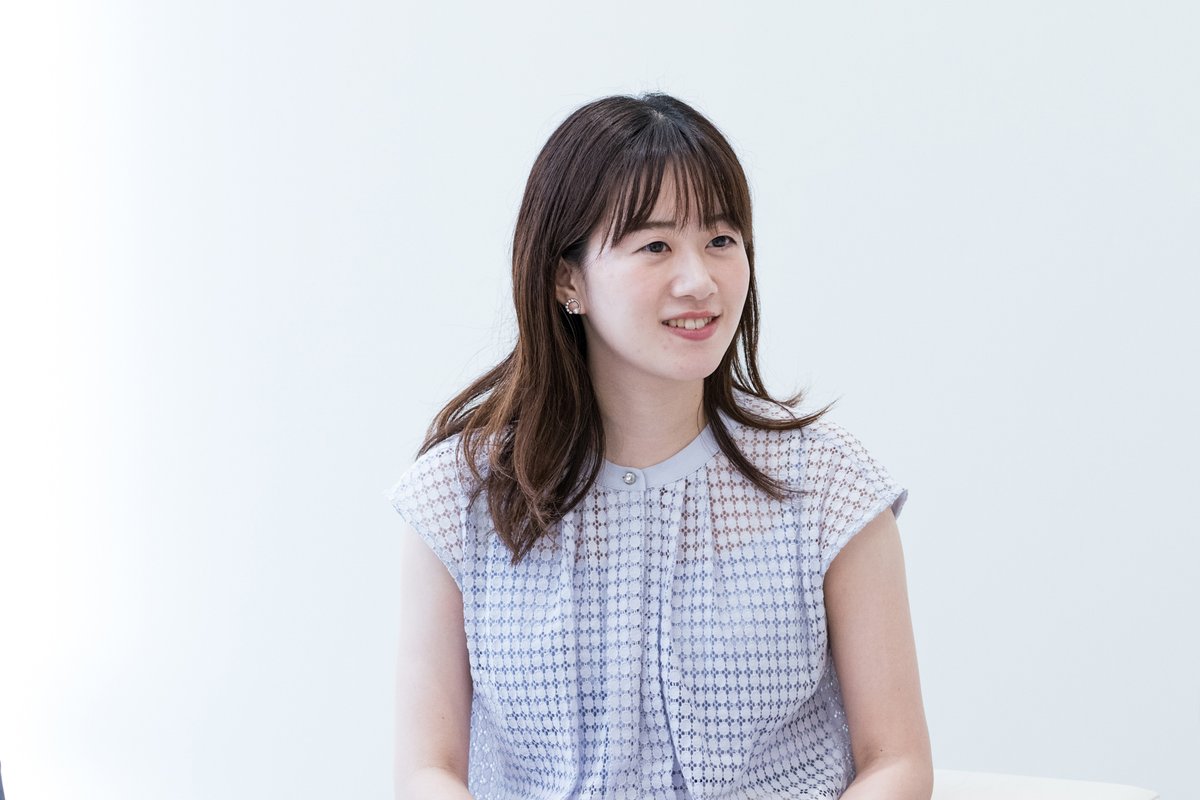
柴田 彩友美
東レ株式会社 機能樹脂事業部 東京機能樹脂第1課 営業担当
2020年入社後、樹脂グローバルオペレーション室にて、ナイロン樹脂やABS樹脂の生産計画・在庫管理を担当。2023年6月に現部署に異動後、デリバリー研修を経て、10月からナイロン樹脂・PBT樹脂・LCP樹脂の営業を担当。
主な担当用途は、住設・建材、文房具、化粧品、コネクター。
営業として、新素材の開発や新用途探索、環境配慮材の提案にも携わる。

小宮 健
東レ株式会社 化成品研究所 樹脂研究室 研究員
2015年東レ入社、樹脂研究室にて汎用エンプラからスーパーエンプラまで様々な樹脂の研究開発を経て、環境対応樹脂の研究開発に着手し、ポリアミド4微粒子の開発に成功。現在はポリアミド4微粒子上市に向け技術部・事業部と協力して基礎研究からスケールアップ、顧客紹介まで開発全般を推進。
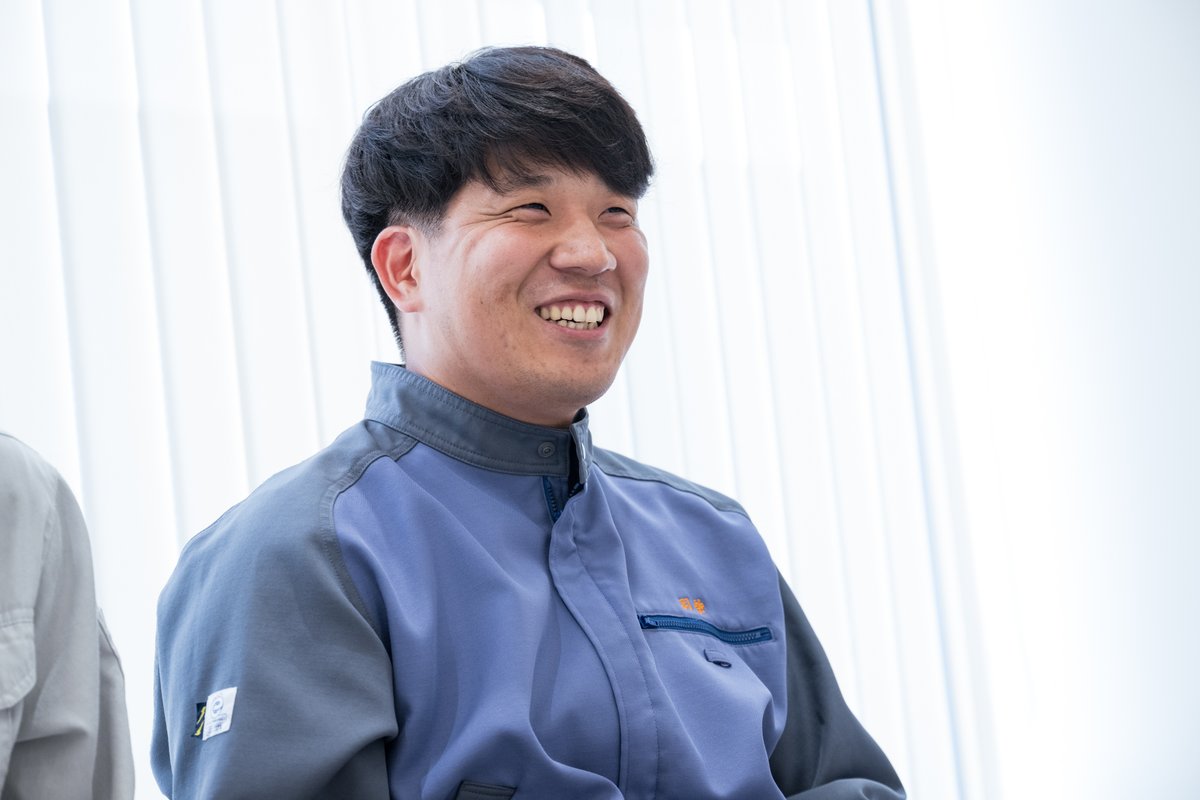
羽柴晃輝
東レ株式会社 メンブレン技術部
2020年東レ入社、ケミカルプロセス技術部にてナイロン樹脂生産工程の設備増強や工程・品質改善などの業務を経て、2021年からはポリアミド4微粒子開発を担当。ラボの基礎研究を工業化するスケールアップをメインに推進してきた。2024年3月にメンブレン技術部に異動し、現在は海水淡水化などに使用される逆浸透膜の開発を行っている。
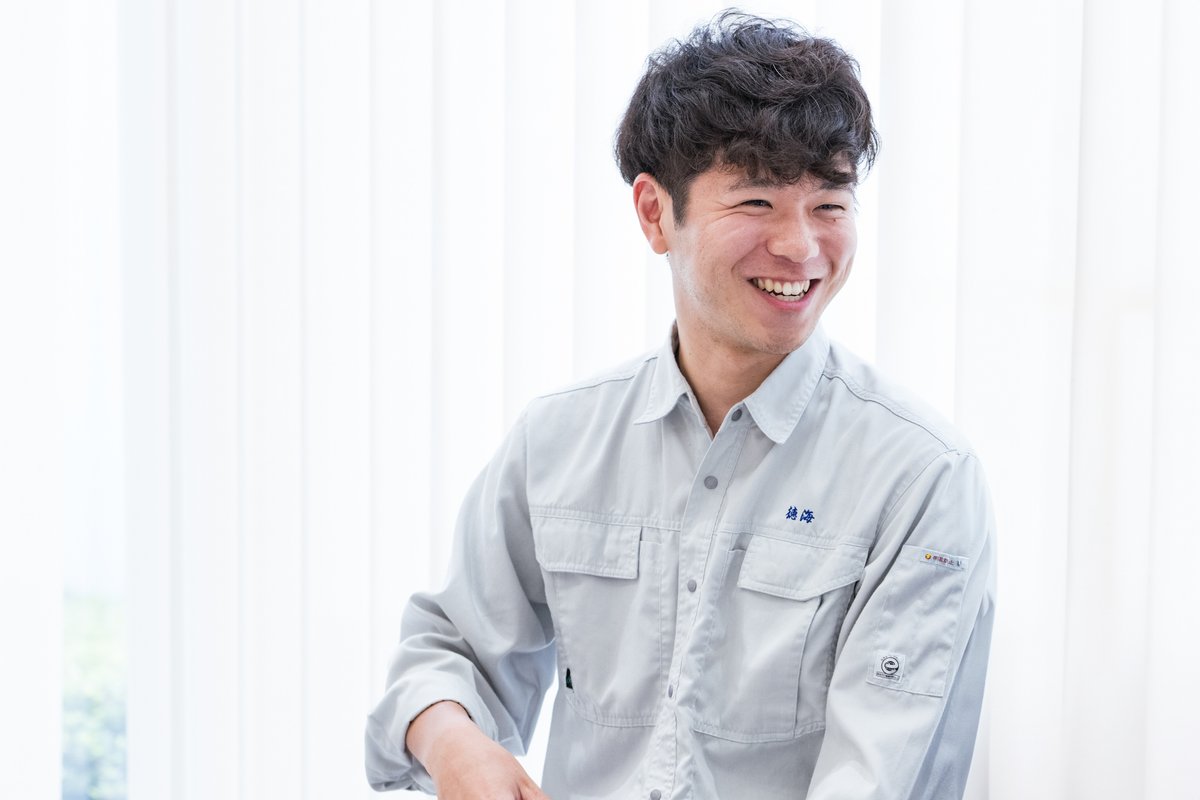
徳海裕也
東レ株式会社 ケミカルプロセス技術部
2021年東レ入社、ケミカルプロセス技術部(東海駐在)に配属され、肥料(コンパクション硫安)の技術開発業務やナイロン6原料(カプロラクタム)製造工程の高度制御導入・適用拡大に従事。部内異動により2023年3月からポリアミド4微粒子の技術開発を担当することになり、主に量産技術開発、サンプル試作、生産体制構築を担当。